Why it’s important to Review your Work Equipment
Work equipment is any machinery, appliance, apparatus, tool, or installation for use at work. This includes equipment which employees have provided for their own use at work. The scope of work equipment is extremely wide, including appliances such as vacuum cleaners. Club owners need to understand the regulations that apply to vacuums cleaners in order to reduce risk of damage liability in case the unexpected were to happen.
The use of work equipment is also very widely interpreted – it covers any activity involving work equipment – such as; starting, stopping, programming, setting, transporting, repairing, modifying, maintaining, servicing, and cleaning.
At Club Insure we’ve listed a variety of regulations, most of which apply to vacuum cleaners. Following these tips will ensure your club remains safe and reduces risk.
Regulations on Work Equipment for Pubs and Bars
- Ensure the equipment is constructed or adapted to be suitable for the purpose it is used or provided for
- Take account of the working conditions and health and safety risks in the workplace when selecting work equipment
- Ensure work equipment is only used for suitable purposes
- Ensure work equipment is maintained in an efficient state, in efficient working order and in good repair
- Where a machine has a maintenance log, keep this up to date
- Where the safety of work equipment depends on the manner of installation, it must be inspected after installation and before being put into use
- Where work equipment is exposed to deteriorating conditions liable to result in dangerous situations, it must be inspected to ensure faults are detected in good time so the risk to health and safety is managed
- Ensure that all people using, supervising, or managing the use of work equipment are provided with adequate, clear health and safety information. This will include, where necessary, written instructions on its use and suitable equipment markings and warnings
- Ensure that all people who use, supervise, or manage the use of work equipment have received adequate training, which should include the correct use of the equipment, the risks that may arise from its use and the precautions to take
- Where the use of work equipment is likely to involve a specific risk to health and safety, ensure that the use of the equipment is restricted to those people trained and appointed to use it
- Where the use of work equipment is likely to involve a specific risk to health and safety, take effective measures to prevent access to dangerous parts of machinery. This will normally be by fixed guarding, but where routine access is needed, interlocked guards may be needed to stop the movement of dangerous parts. Where this is not possible, such as with the blade of a circular saw, it must be protected as far as possible, and a safe system of work used.
- Take measures to prevent or control the risks to people from parts and substances falling or being ejected from work equipment, or the rupture or disintegration of work equipment
- Ensure that the risks from very hot or cold temperatures from the work equipment or the material being processed or used are managed, to prevent injury
- Ensure that work equipment is provided with appropriately identified controls for starting, stopping, and controlling it, and that these control systems are safe
- Where appropriate, provide suitable means of isolating work equipment from all power sources
- Ensure work equipment is stabilised by clamping or otherwise, to avoid injury
- Take appropriate measures to ensure maintenance operations on work equipment can be carried out safely while the equipment is shut down, without exposing people to risks when undertaking maintenance operations
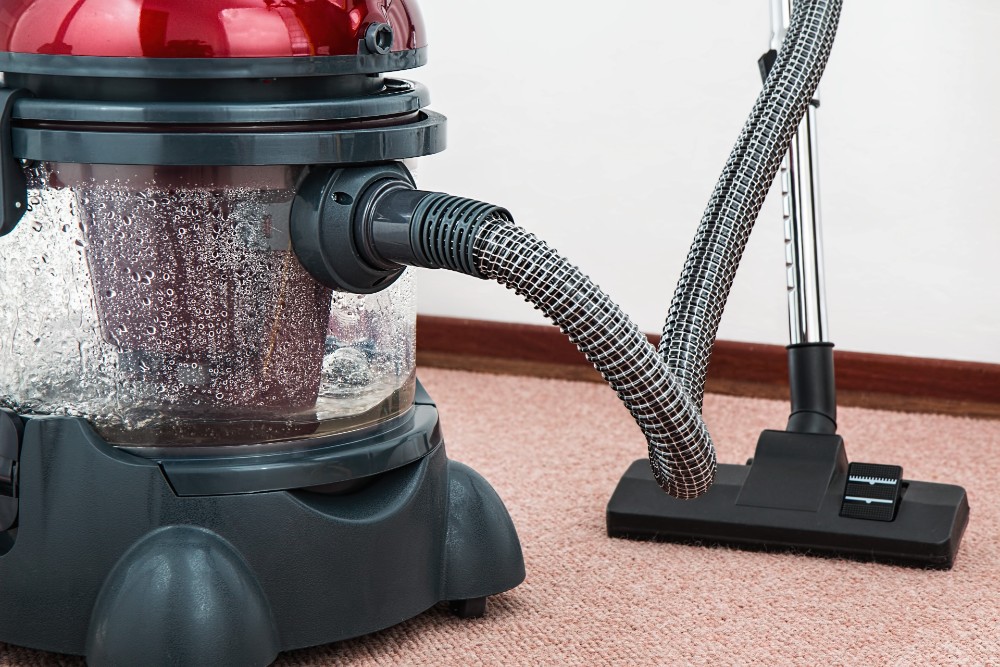
Use of Work Equipment Regulations
Don’t buy any piece of work equipment that isn’t suitable for the job. Anyone using a vacuum must be trained – you may not need a full Safety Operating Procedure but you will most certainly need some clear do’s and don’ts. Ensure that training is recorded just in case the vacuum is used wrongly and results in an injury.
The vacuum will no doubt run on electricity and so falls under the The Electricity at Work Regulations. ‘Electrical equipment’ includes every type of electrical appliance, so ensure you inspect all equipment including the vacuum at the appropriate intervals. Ensure you have all your electrical appliances PAT tested. Contact Club Insure to learn how to get your work equipment PAT tested.
Teach employees not to over stretch cables or knot them. If any equipment is faulty, ask employees to fill out a Defect Report form. Remove the plug from equipment so it cannot be mistakenly used and cause issue. A faulty vacuum can be a fire hazard, it’s important to take away access and ensure it is unplugged after every use.
Do a Workplace Equipment Review
Take a look around your workplace and see if you have an invisible piece of equipment lurking in a cupboard that you never gave a second thought to. Ensure only the equipment you have checked, PAT Tested, and instructed for are available to your employees so as to not leave your business open to risk.
For a full risk assessment, see our risk assessment services at Club Insure. Our innovative approach provides customers with the support, confidence and ability to independently manage their business’s health & safety, risk management procedures and employment issues.